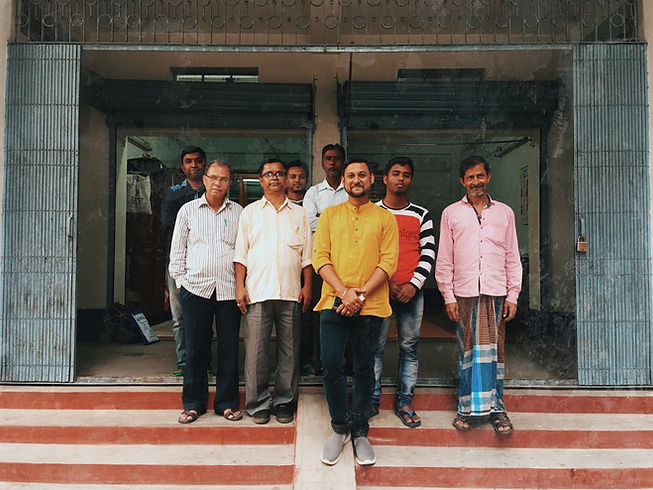
HANDLOOM LINEN
artisans & process
A few hours travel by train from the bustling metropolis of Kolkata in West Bengal, lays the town of Phulia. This town has been renowned as a centre of excellence in hand weaving since Partition when hundreds of skilled weavers migrated here from Bangladesh.
​
​
Seeking new lives, they established themselves in Phulia, building hand looms and specialising in complex weaves like jacquard and jamdani, which are designs based on their Tangail sari culture of their home towns.
​
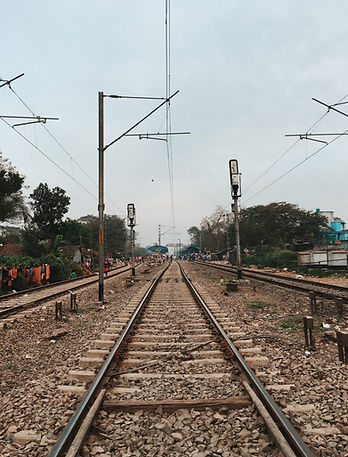

​
Our artisan partners
From the late 1950s, weavers began to form cooperative societies to organise and better market their products. Our weaving partner, one such village weaving society, was established on 24th March 1958 by 52 local weavers.
​
Today the society consists of 213 member weavers and workers, hailing from the villages scattered around town; while it’s predominantly men who sit at the looms, the bulk of pre-and post-loom work is carried out by women.
​
Around 15 of the oldest members are Master Weavers - those who are able to weave more complex patterns or hard to handle yarns, who innovate with new fibres, designs and techniques, and who are able to train the younger weavers.
​
​
The society is managed by a small group of administrators and a president, who are themselves weavers. The complex consists of a long shed containing 100 looms, a back room for spinning bobbins, a showroom and office, and a small house where one of the weavers - Jhuran Das, who also doubles as a groundskeeper - lives with his family.
Looms are a mix of traditional pit looms - which are made by building the loom’s frame above a pit dug into the ground (and which are best suited to enable weavers to stay cool doing the soaring summer temperatures), and standing looms.
​
Working from 10 to 6 every day with Tuesdays off, weavers wages are set by the society according to the level of complexity of the weave. A base daily salary is Rs.500 (USD 7).
​
​


​
​
Jhuran Das, pictured below, is one of the oldest members of the society. At 60 years of age, he is a master weaver who has 45 years of weaving experience behind him. Together with his wife, he lives on the society compound, weaving by day and acting as groundskeeper by night. Like many of his fellow weavers, his father migrated from Bangladesh at the time of partition.
​
​
​
Jhuran took a weaving training course when he was young and now specialises in the more difficult weaves - he weaves our linen and linen-silk blends, as well as jamdanis.
​
​

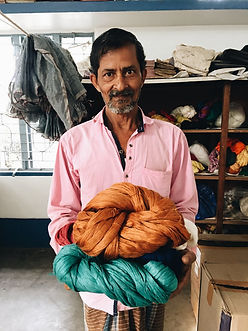


​
In recent decades, the weavers of this society, like everywhere else across the country, have seen the emergence of a major challenge to their livelihoods: the rise of power loom. In 2000, Phulia had around 75,000 handlooms. This declined to 35,000 in 2010 and today there are less than 20,000. An average annual income of a weaving family in Phulia is around 26,000, or USD 350, reflecting low wages and inconsistent work.
The problems arising from power loom are three fold.
The first is that the amount of work available to existing weavers is patchy and inconsistent. The society, who weaves for a wide range of clients, doesn’t receive enough orders to provide full time work to many of the 213 members. When House of Wandering Silk visited the society on a balmy day in February, only three weavers were at the looms - two working on our order of silk-linen jamdani saris. Demand for handloom has dropped in the face of cheap and prevalent power loom cloth.
​
Secondly, younger workers are not interested in hand weaving - they prefer to join a factory making power loom fabrics. The salary is similar to the base salary for hand weaving and yet the amount of work manning a power loom - monitoring the machine and flipping a switch now and again - is significantly less than sitting at a loom and weaving for 8 hours. The availability of such work is also greater.
​
​
​
This means that not only is the handloom industry approaching a slow death with the absence of new weavers, but also that age old techniques, like the complex jamdani that Indians may still see in their grandmother’s saris, will dye out with the older weavers. We see this already with super-specialised fabrics like 250 count muslin - the number of weavers able and willing to weave this almost unbelievable fine cloth number in the very few. Even the number of weavers in the society who can weave linen - a more brittle and difficult fibre to work with and something that is not traditionally woven in India - is only a few.
​
The final major problem faced by weavers is their low pay. Not only does power loom offer a cheaper alternative to the end customer, in many cases it’s impossible to decipher a power loom from a handloom fabric. So even if a customer wants to buy handloom, they won’t necessarily be able to identify one from the other. The Indian fibre and textile industry is notoriously in-transparent; certifications available to determine handloom are prone to misuse.
​
​

​
​
Curious to explore solutions to these problems, we asked the weavers what could be done. The answer: innovation and complexity.
By skills building - transferring skill from the older generation of master weavers to the younger generation - and focusing on experimentation and the weaving of higher value cloth, hand weavers are able to create fabrics which are not replicable by power looms and which fetch a significantly higher value in the market.
More expensive fibres like linen and zari and complex techniques like jamdani and high count muslins are amongst such examples. The resounding request from the members of the society to House of Wandering Silk - and the design community at large - is for us to provide more such orders. More orders means more work; more work means more stability, more income, and more opportunities for the young.
​
​

​
​
Over the last many years working together with our design partners, a Bengali brother-sister duo with whom we co-design and who coordinate directly with the Society, 12 of these weavers have woven some of our most beautiful fabrics: our lineya linens, handspun jamdanis, linen/silk blends, and metallic zari cloth.
But as a small company with no external financing or bulk-buying customers, as much as we would love to give consistent, large orders to the society, we can only order as much as we can sell. So our challenge to ourselves: choose high value, hand loom fabrics; create high quality, useful and desirable clothing; market it in a transparent and responsible way; and leave our customers totally satisfied and desiring more. That is our role in this chain that connects weavers with the owners of their beautiful creations.
​
​
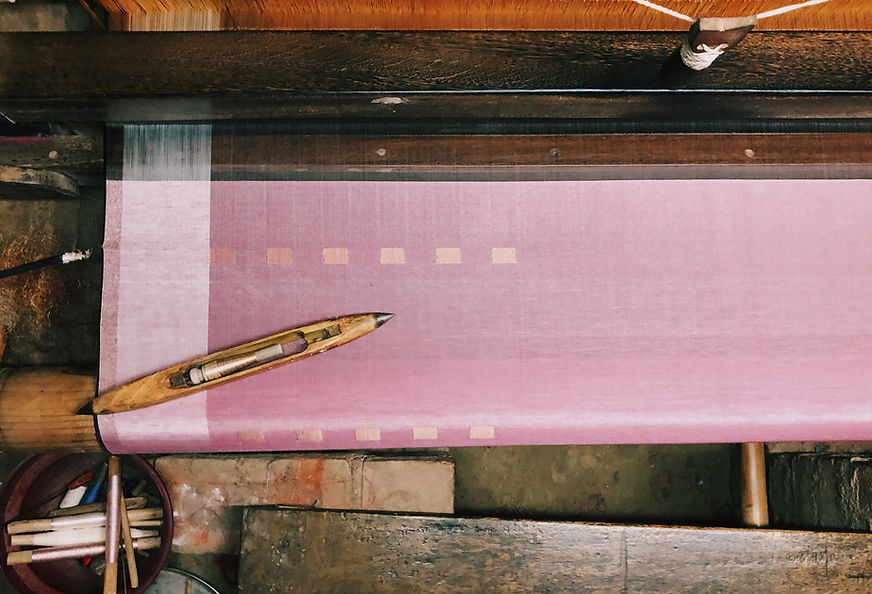
The process / linen
​
​
01
The first step is growing the flax and turning the fibre into yarn. The fibres of the flax plant which are used to create cloth are found under the bark; the outer woody stem must first rot away in a process called retting. In the humid climate of West Bengal, this happens by leaving flax bundles outdoors to rot. These fibres are then dried.
​
A further process of breaking and beating, or scutching, these dried bundles removes the inner, unwanted pith. The remaining linen lengths are combed to straighten them and remove the shorter fibres from the longer ones. Longer fibres are then spun into linen yarn. Our linen yarn is sourced from India's first Flax Mill - Jayashri Mills.
​
​
​
​
02
The yarn is dyed to our colour specifications by a local dyeing unit in AZO free dyes, then collected by the Society who ready the yarn bundles for weaving.
​
​

​
​
03
The society spins the yarn onto bobbins so it can be easily handled. To prepare the yarn for the warp, a laborious process of denting and drafting ensures the correct design will be woven, and drumming the fibre ensures the right tension is achieved.
​
​

​
​
04
Only now can the actual weaving take place. It's done on a pit loom; experienced weavers like Jhuran can weave 3m of linen per day and around 4m of plain weave cotton per day.
​
The finished cloth is washed and ironed before being delivered to House of Wandering Silk.
​
​
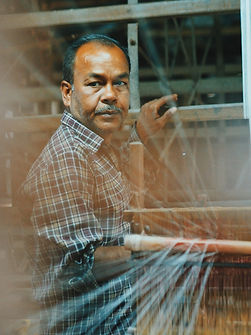

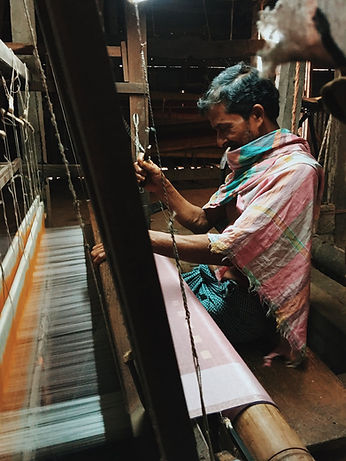

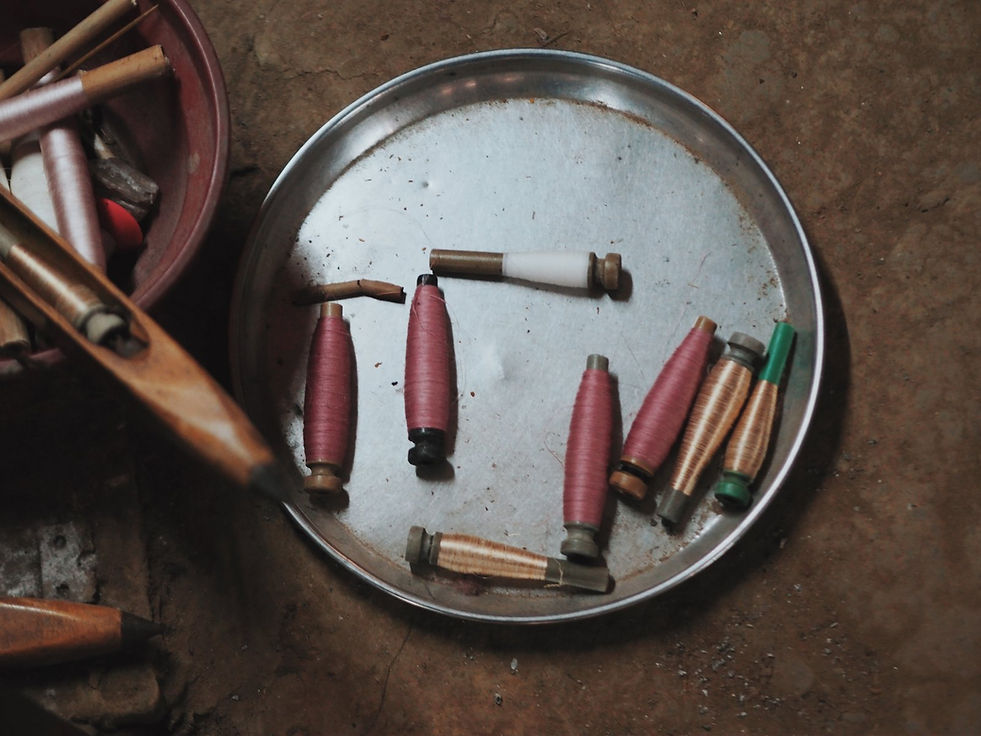