
NAKSHI KANTHA
our artisans & process
​
The earliest and most basic kantha stitch is a simple, straight, running stitch, like the type used on our Kantha Sari Scarves. Over time, however, more elaborate patterns developed, which became known as "nakshi kantha".
Nakshi comes from the Bengali word, naksha, which refers to artistic patterns. Nakshi kantha is made up of motifs influenced by religion, culture and the lives of the women stitching them.
This most humble of cloths gave free reign to the imaginations of the women; kanthas told of folk beliefs and practicies, religious ideas, themes and characters from mythology and epics and the social and personal lives of the artisans; their dreams, hopes and every day village life.
Although there is no strict symmetry to nakshi kantha, the traditional design usually has a lotus as a focal point, with stylised birds, plants, fish, flowers and other scenes surrounding this.
​
​



​
Our artisan partners
Takdira Begum is a 60-something year old lady, hailing from a rural village of West Bengal is eastern India. Passing her in the street, you would never guess from her humble and unassuming manner that she was recipient of multiple national awards, including a Shilp Guru Award in 2009; an award conferred on master craftspeople for innovation in traditional craftsmanship, and recognising the highest level of aesthetic character, quality and skill.
Takdira was married at 19 years old and soon had three daughters. She had a burning desire to create something for herself and her children, but what opportunities are there for a woman in rural India in a conservative, highly patriarchal society?
Takdira possessed a skill which was shared by millions of women across the region: kantha embroidery. Her grandmother and mother had made kantha for their household use and passed the skills down to Takdira from when she was a young girl. Finishing her formal school studies at class 9, aged 14, she continued learning at art school for 2 years, studying all the different stitches, how to make new designs, and how to market her work.
Soon after marriage, Takdira started off by calling a few younger girls in their mid-teens from around her village. She trained them to improve their kantha skills, then hired them to start making kantha fabric for the local market. From the outset, Takdira avoided the most common form of kantha: straight stitches on recycled saris. Instead she embroidered elaborate and complex designs exclusively on hand woven tussar silk, creating new, unique and highly-valued products in her local market.
​
​

HOWS founder, Katherine, with Takdira and her daughter, Runa Laila.
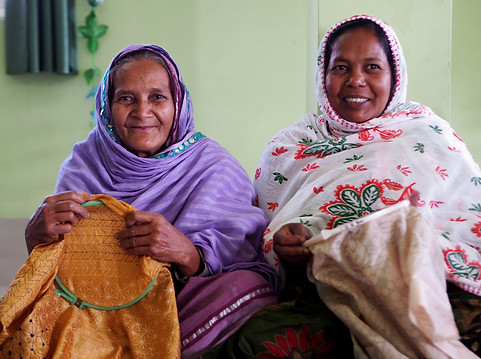
Fine nakshi kantha is a rare art; the time, skill and patience required to create a textile which may take up to 6 months or more to create is uncommon. Passed from mother to daughter, the younger generations are increasingly reluctant to take up this work.
​
In this context, it wasn't easy for Takdira to convince local women to work with her. Even harder was to convince their husbands to allow them to work. Takdira's husband, a kindly and quiet gentleman, supported her from the start, using his influence in the community to encourage his friends to allow their wives to work.
​
The group began to grow, and increasingly local women started approaching Takdira to ask for work. All this effort has paid off! Takdira's group now consists of over 100 women ranging in age from 18 to 70 years, in two clusters in Bardhaman District: one cluster who work on the more "simple" nakshi kantha on running yardage fabric, and a second cluster working on the more elaborate scarves and wraps.
​

Two of Takdira's daughters live out-of-state - one in Delhi and one in Hyderabad. Her youngest daughter, Runa Laila, lives locally. In her thirties and with two children (who are also learning kantha from Takdira), she's been stitching kantha since her teenage years when she learnt from her mother. She's joined the family business and supports Takdira in their main work: creating new patterns and designs for their artisans to embroider. Runa says the part she likes best about the work is meeting different people.
​
The beauty of this work is that not only does it build on the existing skills of the artisans, it fits comfortably between conflicting needs: the desire of the women to work for themselves and earn an independent income, and the demands of their society that they fulfil their expected "traditional" roles.
​
The artisans pick the fabric from Takdira and take it home to work. They can take as long as they need and drop the finished work when it’s done. Some take months, some take up to a year.
We're enormously proud to partner with Takdira Begum who has revitalised this art form in her village.
​
​
Reliquaries of our textile heritage - between them, these 12 ladies possess a combined 261 years of precious kantha skill and experience
​
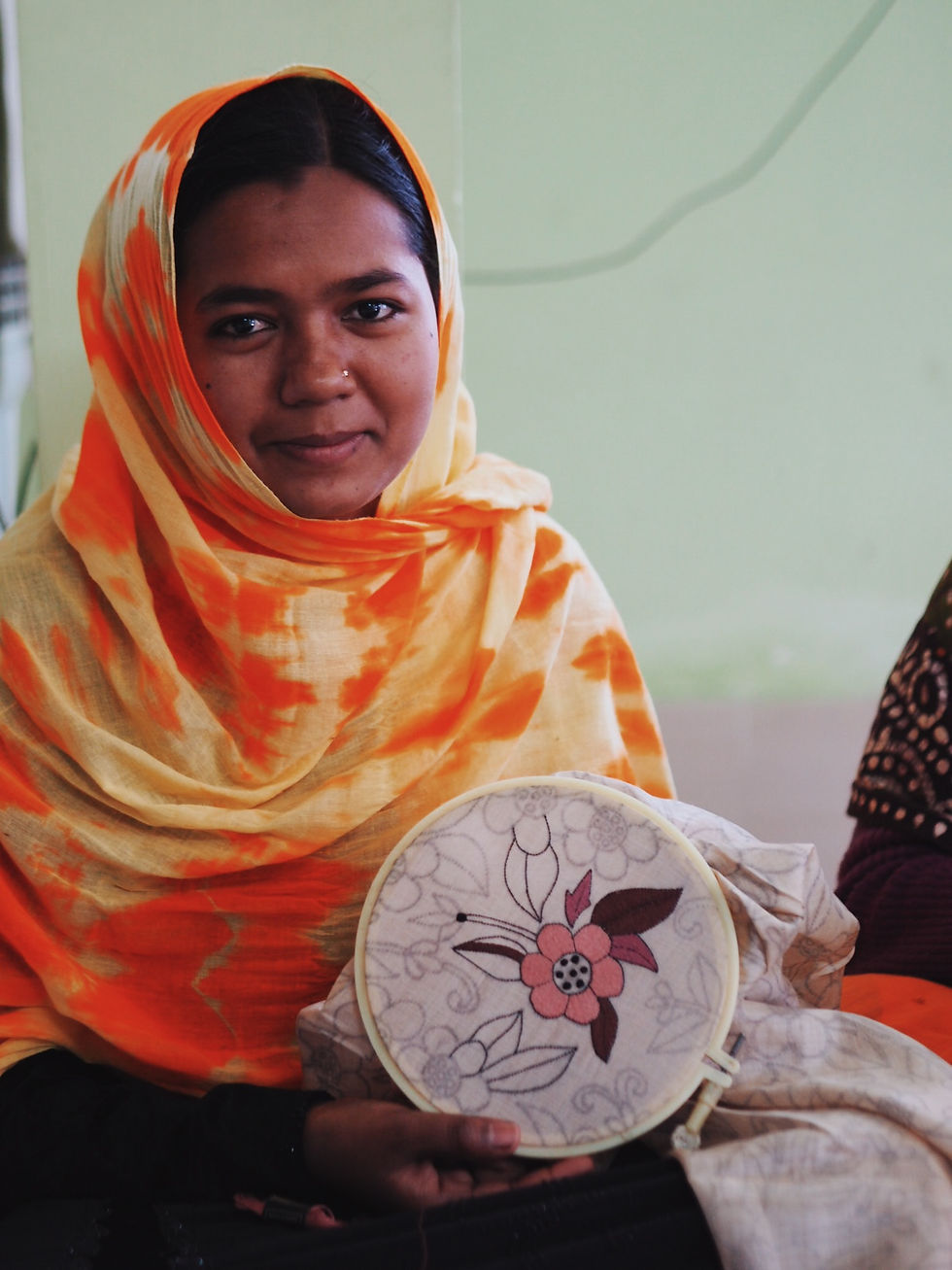



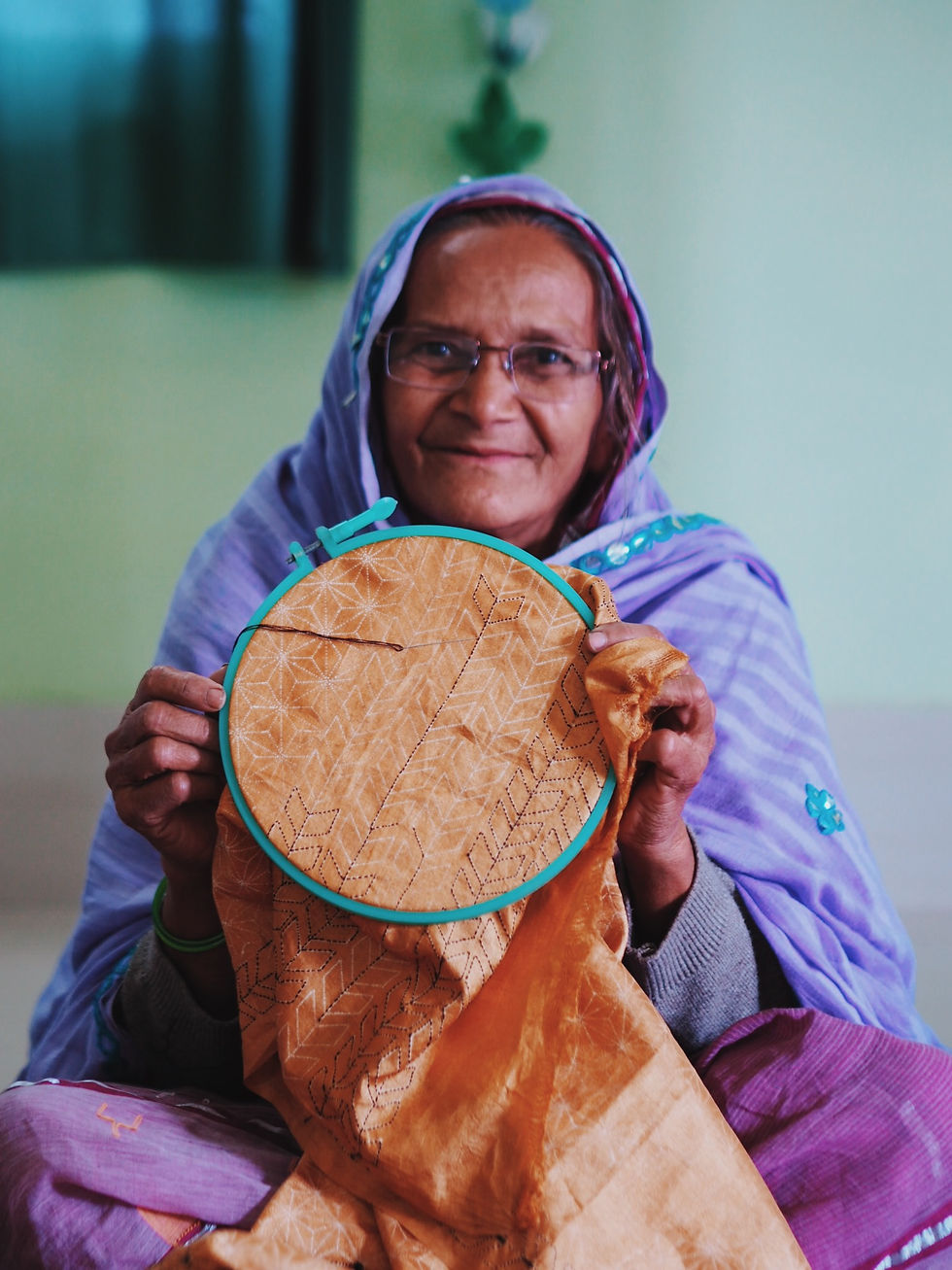





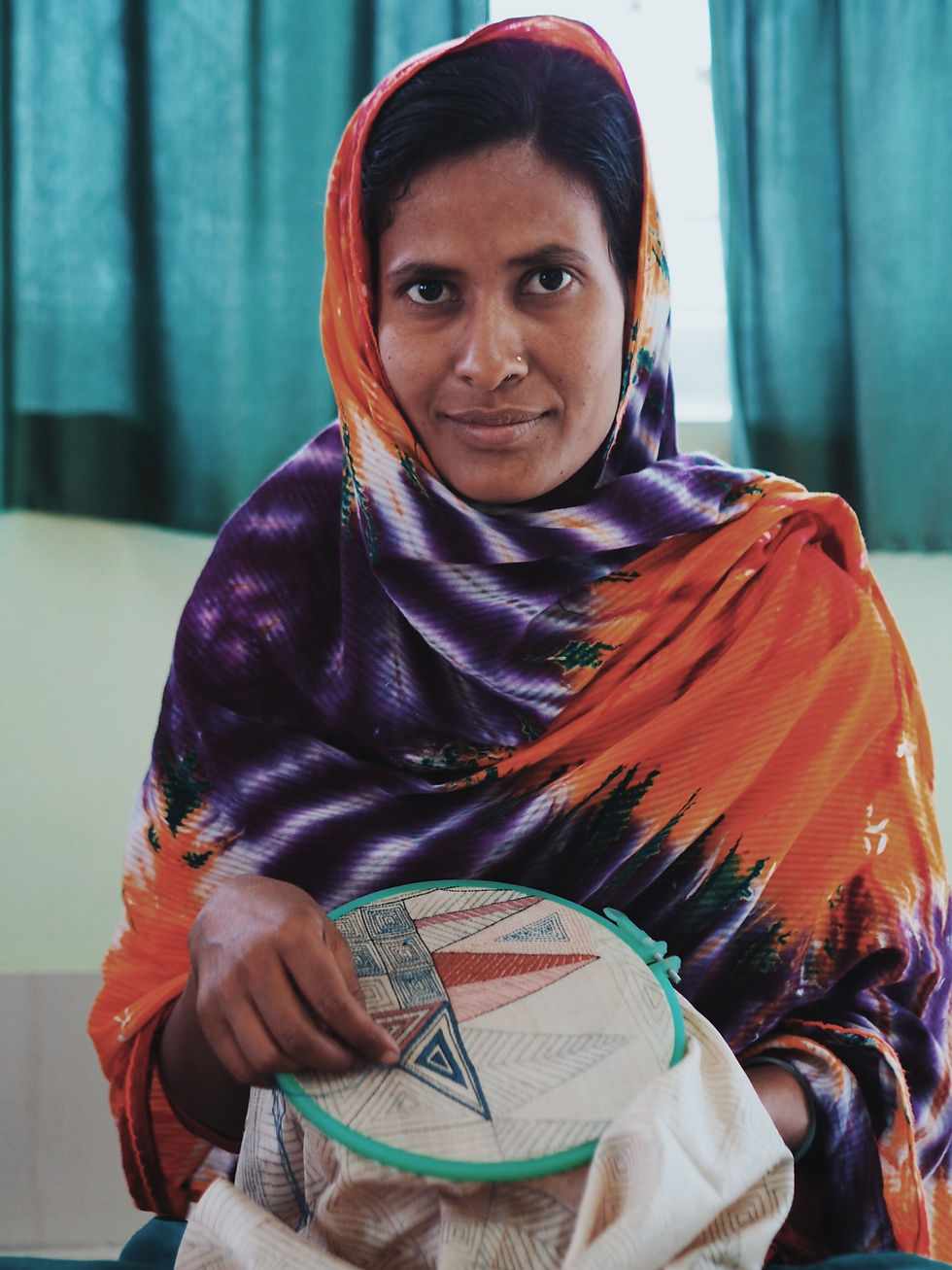

Top row from left: Parul Khatun, age 20 years, 5 years doing kantha - Samsulnihar Sheikh, age 40 years, 23 years doing kantha - Nubika Sheikh, age 58 years, 27 years doing kantha - Gulehar Sheikh, age 60 years, 35 years doing kantha
2nd row from left: Kharunsha Sheikh, age 70 years, 50 years doing kantha - Josona Bibi Sheikh, age 40 years, 20 years doing kantha - Thahirun Sheikh, age 43 years, 20 years doing kantha - Kohinoor Bibi, age 47 years, 22 years doing kantha
3rd row from left: Sheikh Jahanara, age 55 years, 25 years doing kantha - Sarina Khatun, age 20 years, 5 years doing kantha - Khairunnesa Khatun, age 25 years, 15 years doing kantha - Rozina Khatun, age 26 years, 14 years doing kantha.
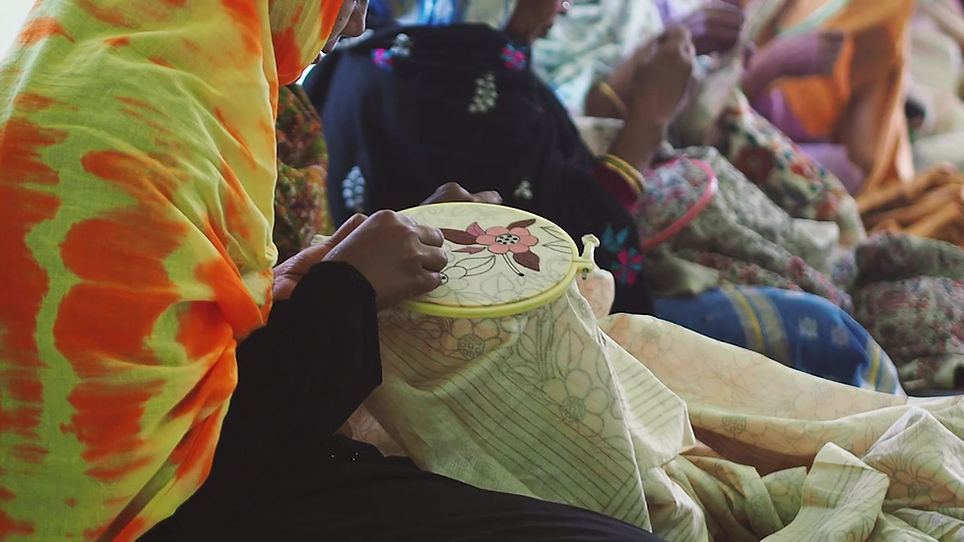
The process
01
Takdira and Runa sketch out their idea for a new design on a piece of art paper, before transferring the final design onto tracing paper. The lines are neatly and cleanly drawn on in pencil. It could be a more straight-forward geometric pattern for the yardage, or a finely detailed design for a scarf.



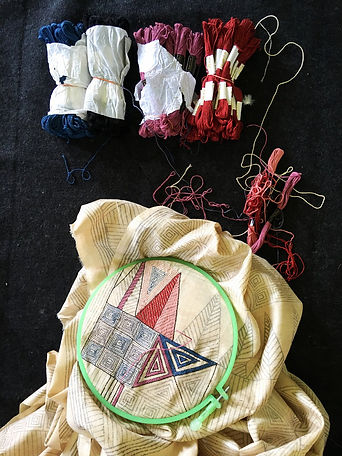
For design ideas, they don’t look to outside trends or ideas; Takdira and Runa come up with their own ideas which they evolve over time. Takdira sets the amount to be paid to the artisan based on the complexity and amount of work. This takes around five days.
​
02
One of the artisans, specially trained in this task, will prick thousands of tiny pin holes along all the design lines. A small pin stuck in bit of bamboo is used for this - the bamboo makes it easier for the artisan to hold. This takes around one day.
03
The hand woven tussar silk, which has been bought by Takdira directly from the local weavers, is ironed and cut to size. On long tables, the fabric is laid out with the tracing paper across it.
Fabric dye is mixed with turpentine to make a smooth and washable white paste which is then rubbed across the paper pattern; seeping through the pin pricks onto the cloth below, it marks out the design with tiny white dots. This takes an hour or two.
​
​
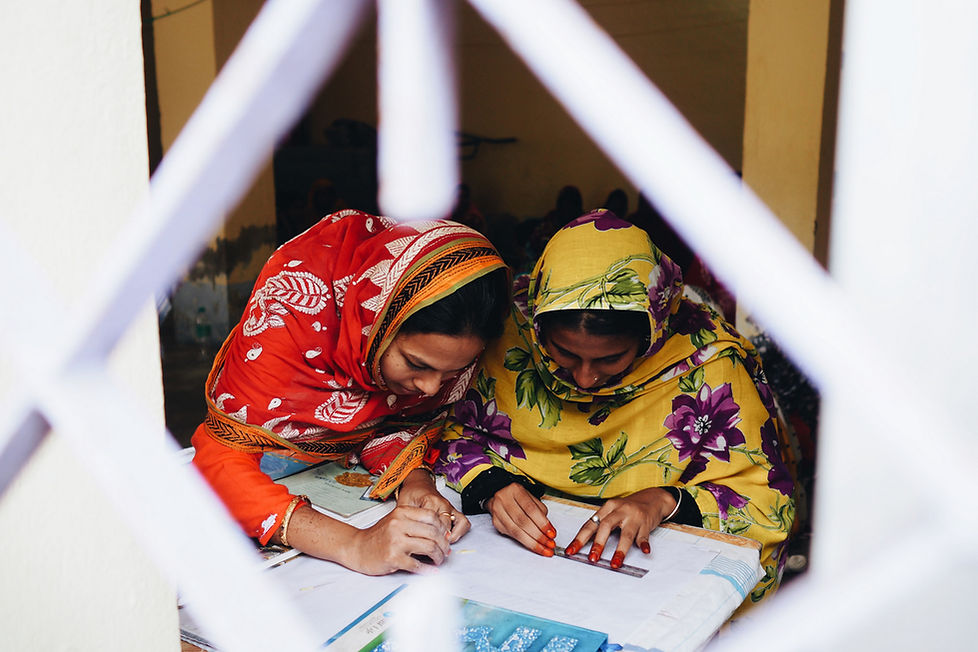

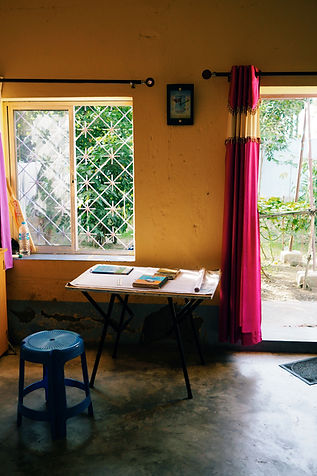

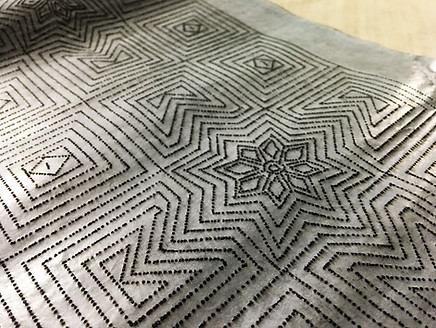





​04
Takdira and Runa will then match each fabric with the cotton anchor thread required to embroider it; so not only does the design come from them, but also the colour story for each piece of work.
The fabric is distributed to the artisans for stitching - one woman will work on one cloth. The more skilled the artisan, the more complex the work given to her is. Taking the fabric home, she'll work when she can, between household chores and caring for her family - usually between 2-5 hours per day.
​
​
The kantha embroidery itself is done with 2 anchor threads and a needle - the most simple of tools. Fine running stitch is made through small jabs into the cloth, held taught by a bright, plastic embroidery frame. The artisans are incredibly adroit; they can embroider the smallest of stitches very quickly. Finished work is brought back to Takdira's house and the artisan is paid.
​
​
A smaller, "simpler" scarf will take around 2 months to embroider. The more elaborate wraps will take upwards of 3 or 4 months, with many pieces requiring 6 months of dedicated work.

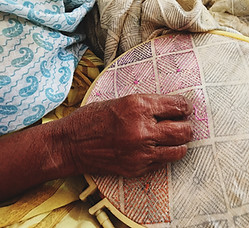
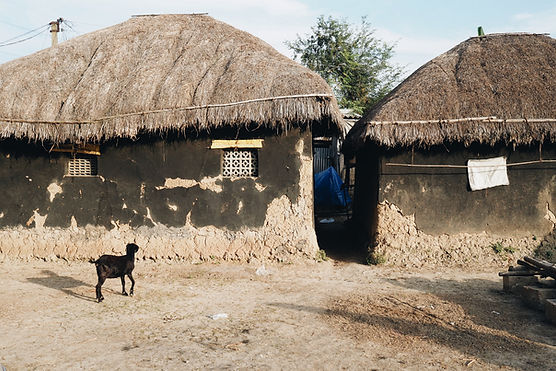

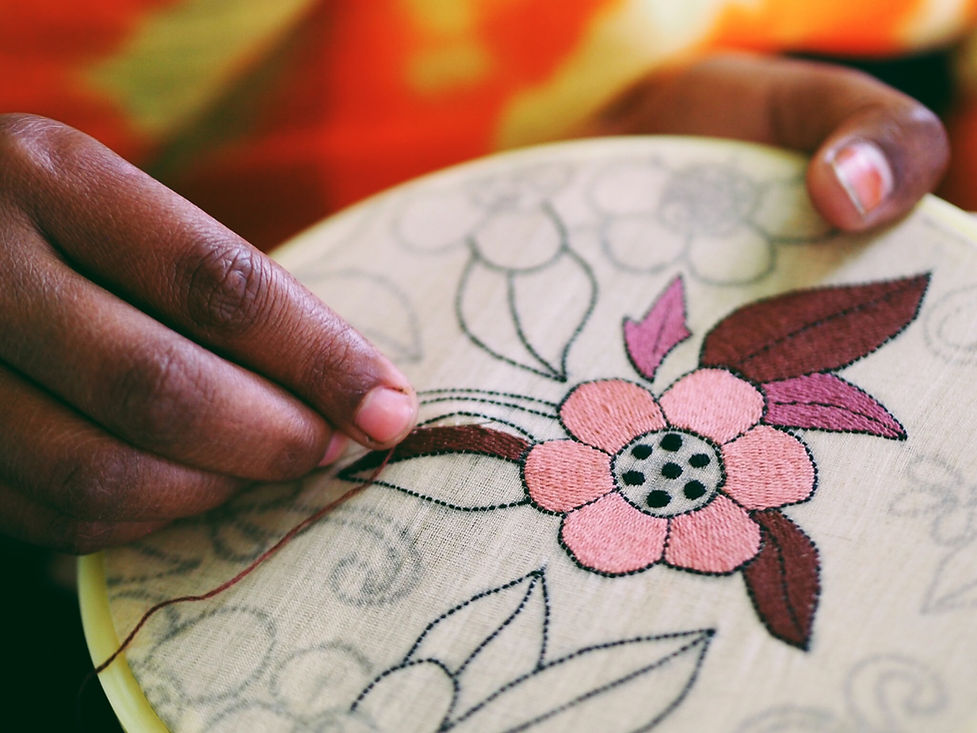


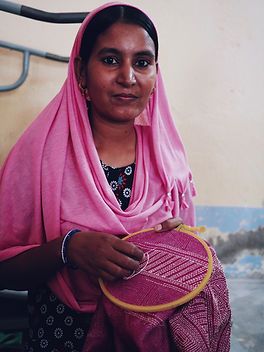



05
When the cloth comes back - after months and months of work - it's in need of a wash. The cloth will be hand washed several times to remove dirt and the feint trace lines. After ironing, the tussar silk is crisp and clean .
​
​
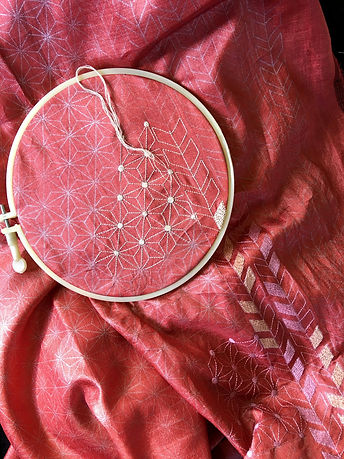

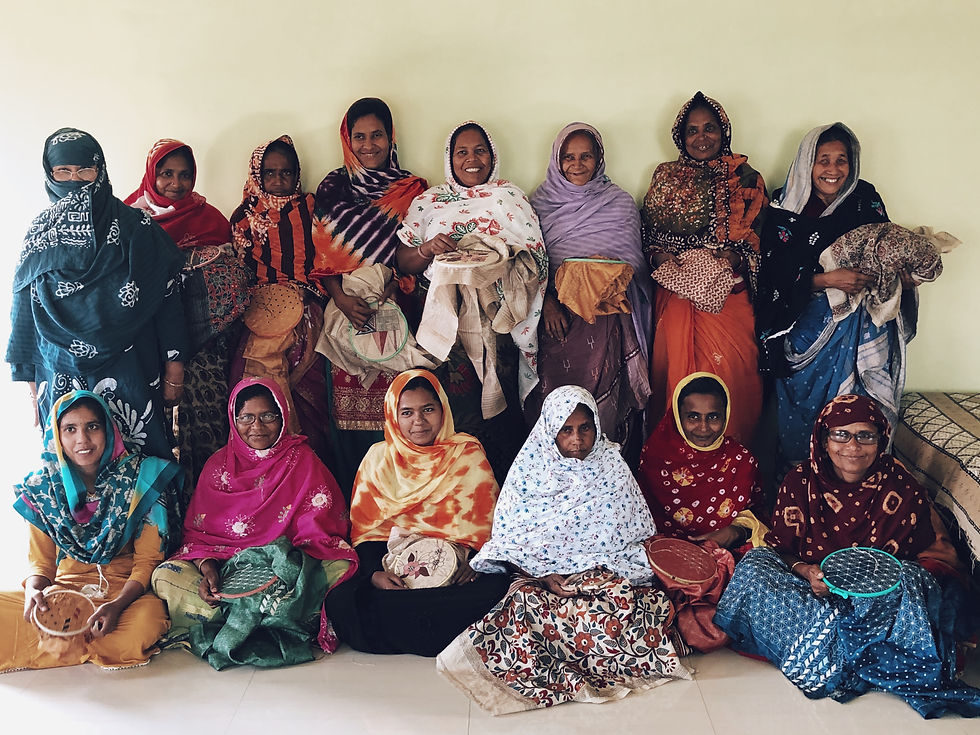